Risikomanagement
Risiken beherrschen und minimieren (Teil 2)
Risikomanagement und Risikobeurteilung sind Begriffe, die in der Praxis in vielen Unternehmen und Organisationen an Bedeutung gewinnen. Doch wie kann es gelingen, das Risiko zu beherrschen und zu minimieren? In Teil 1 (siehe SICHERE ARBEIT 4/2020, Seite 40 ff.) stand Risikomanagement als Führungsaufgabe im Fokus. In diesem Teil geht es um die Risikobeurteilung von Maschinen.
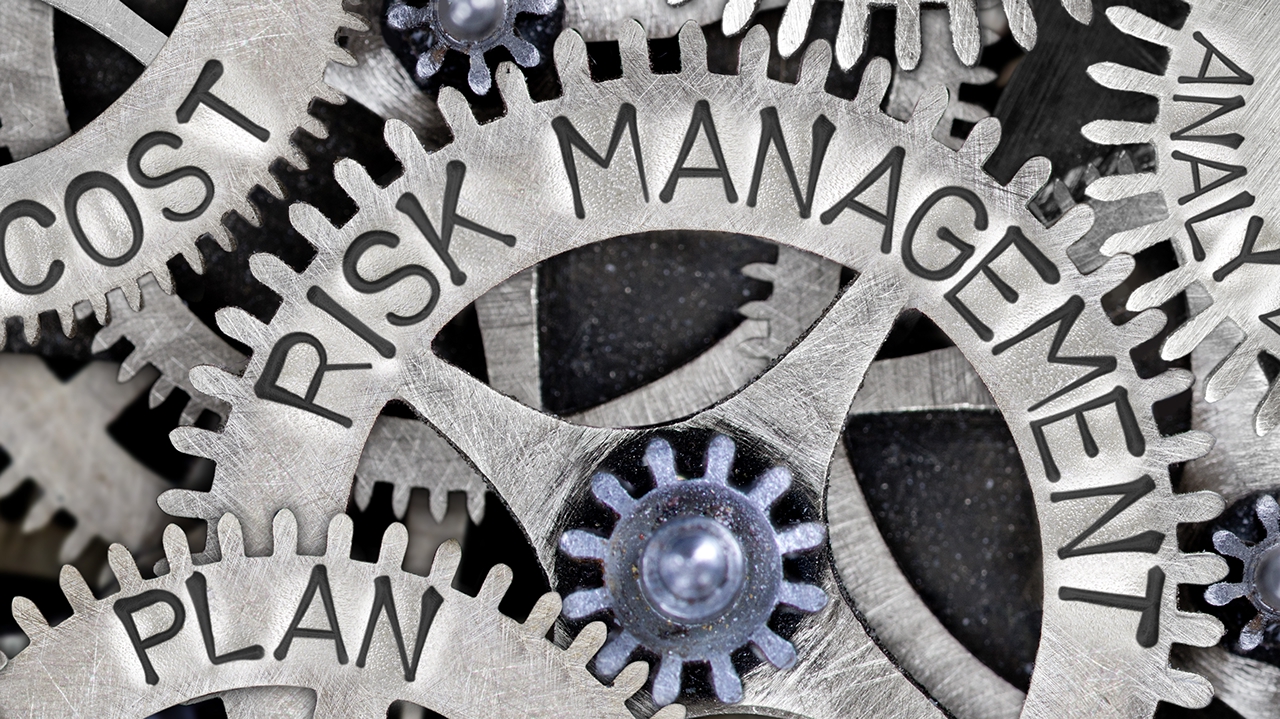
Für die Durchführung einer Risikobeurteilung von Maschinen wird von Herstellern die europäisch harmonisierte Norm ÖNORM EN ISO 12100 (Sicherheit von Maschinen – Allgemeine Gestaltungsleitsätze – Risikobeurteilung und Risikominderung) herangezogen. Sie enthält einen Leitfaden zur Risikobeurteilung sowie im Anhang Checklisten von Gefährdungen und Belastungen, die für eine Risikobeurteilung des Herstellers sehr hilfreich sind. Folgende Punkte müssen im Rahmen einer Risikobeurteilung von Maschinen beachtet werden:
- Festlegen der Grenzen der Maschine
- Identifizieren der Gefährdungen
- Risikoeinschätzung
- Risikobewertung
- Festlegen von Maßnahmen
Zu den Grenzen einer Maschine gehören:
- Verwendungsgrenzen
- räumliche Grenzen
- zeitliche Grenzen
- weitere Grenzen
In Bezug auf Verwendungsgrenzen von Maschinen sind folgende Überlegengen anzustellen:
a) die unterschiedlichen Lebensphasen einer Maschine (bestimmungsgemäße Verwendung, Wartung, Instandhaltung, Rüsten, Störungsbehebung, unterschiedliche Betriebsarten, Störungsbehebung, Transport, Montage, Installation, Außerbetriebnahme, Demontage, Entsorgung … )
b) Eingriffsmöglichkeiten durch den Anwender bzw. Anzahl der Bedienplätze
c) Ausbildung für den Anwender in Hinblick auf spezielle Schulungen
Zu den räumlichen Grenzen gehören:
a) Bewegungsraum
b) Platzbedarf von Personen
c) Wechselwirkungen zwischen Mensch und Maschine
d) Schnittstelle Maschine/Energieversorgung
Unter zeitlichen Grenzen ist zu verstehen:
a) Grenze der Lebensdauer der Maschine und/oder einiger ihrer Bauteile
b) empfohlene Wartungsintervalle
Zu den weiteren Grenzen zählen:
a) Mindest-/Höchsttemperaturen,
b) Eigenschaften von zu verarbeitenden Materialien
c) besonderer Grad an Sauberkeit
Der nächste Verfahrensschritt ist die Ermittlung von Gefährdungen in den einzelnen Bereichen. Dazu zählen neben den mechanischen, chemischen, elektrotechnischen und steuerungstechnischen Gefährdungen auch die Belastungen durch Lärm und Vibrationen sowie ergonomische Anforderungen, die zu berücksichtigen sind. Im nächsten Schritt ist für jede Gefährdungssituation eine Risikoeinschätzung durchzuführen. Das mit einer bestimmten Gefährdungssituation zusammenhängende Risiko hängt von folgenden Elementen ab:
Schadensausmaß:
a) Ausmaß der Verletzungen/Gesundheitsschädigung (z. B. leicht, schwer, tödlich)
b) Schadensumfang (z. B. eine Person oder mehrere Personen betroffen)
- Eintrittswahrscheinlichkeit des Schadens
- Gefährdungsexposition von Personen (exponierte Personengruppen)
- Eintritt von Gefährdungsereignissen
- Möglichkeiten zur Vermeidung oder Begrenzung
- Art, Häufigkeit und Dauer der Gefährdungsexposition
Die Einschätzung jeder Gefährdungsexposition bzw. Gefährdungssituation erfordert eine Analyse aller Betriebsarten und aller Lebensphasen der Maschine. Insbesondere muss die Analyse das Erfordernis eines Zugangs während Einrichtung, Einlernen (Teachen), Umrüstung oder Prozesskorrektur, Reinigung, Fehlersuche und Instandhaltung berücksichtigen. Die Risikoeinschätzung muss auch Aufgaben berücksichtigen, für die Schutzmaßnahmen zeitweilig aufgehoben werden müssen.
Unterschiedliche Verfahren zur Risikoeinschätzung
Die Verfahren, die im Rahmen der Risikoeinschätzung herangezogen werden können, sind vielfältig. Dabei können qualitative, quantitative oder semi-quantitative Verfahren zum Einsatz kommen. Bei der qualitativen Methode wird das Risiko ohne Zugrundelegung eindeutig definierter Größen beschrieben. Dabei werden Kennwörter wie „gering“, „hoch“, „selten“ oder „häufig“ verwendet. Bei der quantitativen Variante wird hingegen das Risiko unter Zugrundelegung von definierten Bezugsgrößen definiert, wie zum Beispiel der Eintrittshäufigkeit (Ereignisse pro Zeiteinheit, absolut oder prozentuell) und der Auswirkung des Ereignisses, welches meist monetär bewertet wird. Bei einer semi-quantitativen Methode werden Kennzahlen, wie es zum Beispiel bei einer FMEA-Analyse (FMEA = Fehlermöglichkeits- und Einflussanalyse) der Fall ist, herangezogen. FMEA verwendet die Risikoprioritätszahl (RPZ) zur Risikoeinschätzung. Die Maschinenrichtlinie geht nicht auf die Verfahren der Risikoeinschätzung, die ein Hersteller zu verwenden hat, ein. Ganz allgemein können folgende Verfahren für eine Risikoeinschätzung zur Anwendung kommen:
- Brainstorming
- Frühinformationssysteme
- Szenariotechnik
- Fehlermöglichkeits- und Einflussanalyse (FMEA)
- Fehlerbaumanalyse (FTA)
- Ereignisbaumanalyse (ETA)
- Checklisten, Prüflisten
- Schadensfalldatenbank
- Walkthrough
- Befragungen
- Analyse von Dokumenten
- Recherchen (Märkte, Trends, Technologie, Compliance …)
- Risikomatrix
- Risikographen
- HAZOP (HAZard and OPerability analysis)
- HACCP (Hazard Analysis and Critical Control Points)
- Bow-Tie-Analyse
- What-if-Analyse oder SWIFT-Analyse (Structured What-if Technique)
In der Praxis haben sich im Zusammenhang mit Maschinen zur Risikoeinschätzung die Verfahren der FMEA, eine Risikomatrix, der Einsatz von Checklisten oder das Heranziehen von Risikographen als geeignet gezeigt.
FMEA
Unter der Fehler-Möglichkeits-Einfluss-Analyse (FMEA) versteht man ein strukturiertes, im Team durchzuführendes Verfahren. Dabei werden unterschiedliche mögliche Gefährdungen erfasst und mit einer sogenannten Risikoprioritätszahl (RPZ) versehen. Diese Risikoprioritätszahl (RPZ) ist von drei Einflussfaktoren abhängig:
- Bedeutung, bezieht sich auf die Schwere einer auftretenden Verletzung
- Auftretenswahrscheinlichkeit eines Ereignisses
- Entdeckungswahrscheinlichkeit
RPZ = B × A × E
Die einzelnen Zahlenwerte für B, A und E entnehmen Sie der Abbildung 1.
Jeder einzelne Parameter ist nach einer Skala von 1 bis 10 zu bewerten. Die Höchstsumme der Risikoprioritätszahl (RPZ) hat demnach den Wert 1000. Im Rahmen der Risikoeinschätzung ist den jeweiligen Gefährdungen ein Zahlenwert zuzuordnen. Danach wird im Rahmen der Maßnahmenfestlegung beurteilt, inwieweit eine Handlung zur Minderung des Risikos notwendig wird. Ein Vorteil dieser Variante bzw. Methode besteht darin, dass anschaulich die Höhe des jeweiligen Risikos dargestellt werden kann. Je höher der Zahlenwert, desto größer das Risiko und desto aufwendigere Maßnahmen zur Risikominderung müssen gewählt werden.
Risikomatrix
Eine weitere in der Praxis gerne genutzte Variante zur Risikoeinschätzung von Maschinen ist das Verfahren mithilfe der Risikomatrix. Dabei handelt es sich um eine zweidimensionale Darstellung, bei der auf einer Achse das Schadensausmaß, auf der anderen die Eintrittswahrscheinlichkeit aufgetragen wird (siehe Abbildung 2).
Dabei bedeutet die Farbe Rot ein hohes Risiko. Dieses muss bevorzugt durch konstruktive Maßnahmen reduziert werden. Nur in Einzelfällen, wenn es der Prozess (Arbeitsprozess) nicht zulässt, dürfen andere Maßnahmen zur Risikominderung herangezogen werden. Die Farbe Gelb bedeutet ein geringeres Risiko als Rot. Dieses kann entweder konstruktiv oder durch technische Schutzmaßnahmen reduziert werden. Mit der Farbe Grün werden Restrisiken gekennzeichnet, die keine weiteren (konstruktiven) Maßnahmen erfordern. Dennoch können qualitätssichernde Maßnahmen oder eine persönliche Schutzausrüstung erforderlich sein.
Vorsicht: Konstruktive Maßnahmen sind nicht zwangsläufig quantitativ messbar.
Beispiel: Ein Risiko durch Quetschen muss grundsätzlich durch einen Eingreifschutz oder ausreichende Abstände verhindert werden. Dies gilt z. B. in den Feldern 3 A und 3 B der Risikomatrix.
Technische Schutzmaßnahmen in Verbindung mit einer Steuerung (Sicherheitsfunktionen) sind durch die geforderte Sicherheitsintegrität (SIL oder PL) qualitativ und quantitativ messbar.
Beispiel: in 3 A kann ein SIL 3 bzw. PL e erforderlich sein, dagegen in 3 B ein SIL 2 oder PL d.
Die Definition des Schadensausmaßes und der Eintrittswahrscheinlichkeit zeigt Abbildung 3.
Risikographen
Neben den bisher kurz beschriebenen Varianten werden häufig auch Risikographen zur Risikoeinschätzung herangezogen. Risikographen findet man häufig auch in europäisch harmonisierten Normen. Ein Beispiel eines Risikographen findet sich in der europäisch harmonisierten Norm ÖNORM EN ISO 13849-1 (Sicherheit von Maschinen – Sicherheitsbezogene Teile von Steuerungen – Teil 1: Allgemeine Gestaltungsleitsätze). Ein solcher ist in Abbildung 5 dargestellt. In dieser Norm wird der Risikograph zur qualitativen Einschätzung der Sicherheitssteuerungsarchitektur verwendet.
Risikobewertung
Im Anschluss an die Risikoeinschätzung folgt die Risikobewertung. Bewertet wird, inwieweit Maßnahmen notwendig werden oder nicht. Ein Maß dafür, ob Maßnahmen gesetzt werden müssen, ist in Normen, Merkblättern oder Regeln der Technik enthalten. Eine Norm muss nicht eingehalten werden, aber das Niveau der Norm ist zu erfüllen. Wenn der Hersteller der Ansicht ist, dass Maßnahmen gesetzt werden müssen, sind diese in der vorgesehenen Hierarchie umzusetzen. Die Reihenfolge an Maßnahmen ist so festgelegt, dass konstruktive vor technischen, organisatorischen und persönlichen Handlungen seitens des Herstellers zu setzen sind.
Wenn zum Beispiel eine technische Maßnahme, wie das Anbringen einer Schutzeinrichtung vor einer Gefahrenstelle, gesetzt wird, dann ist nach der Durchführung dieser Maßnahme eine neuerliche Bewertung der Schutzeinrichtung durchzuführen. Dabei geht es darum, ob diese Schutzmaßnahme zu einer akzeptablen Reduktion des Risikos geführt hat. Falls nicht, oder für den Fall, dass eine neuerliche Gefährdung hinzugekommen ist, müssen Gegenmaßnahmen zur Reduktion des Risikos getroffen werden. Das akzeptable Restrisiko ist jenes, welches der Hersteller oder sein Bevollmächtigter verantworten muss. Ein Maß für das zulässige Restrisiko ist in Normen, falls vorhanden, beschrieben bzw. enthalten. Das Verfahren der Risikobeurteilung im Rahmen der Maßnahmenwahl ist als iteratives Verfahren zu sehen.
Generell ist festzuhalten, dass bei einer Risikobeurteilung nicht bei jeder Betrachtung der Maßnahme bei der jeweiligen Gefährdung das Ergebnis „Restrisiko ist gleich null“ oder „kein Restrisiko mehr vorhanden“ herauskommt!
Abschließend ist festzuhalten, dass bei der Ermittlung von Gefährdungen im Rahmen einer Risikobeurteilung die Maschine oder das Arbeitsmittel noch ohne folgende Maßnahmen zu bewerten ist. Die Maßnahmen sind dann die entsprechenden Lösungen, die zu einer Risikominderung der jeweiligen Gefahrenstelle führen. Wenn es zu einem unerwünschten Ereignis, Schadensfall oder Arbeitsunfall kommt, dann wird eine mögliche Unfallerhebung sehr genau anhand der vorgelegten Analyse durchgeführt.
Fachseminare zur Risikobeurteilung
Wie schon oben angesprochen, gibt es im Großen und Ganzen keine „falschen“ Risikobeurteilungen, Evaluierungen oder Gefahrenanalysen, sondern nur Überlegungen bzw. Analysen, die nicht zeitnah durchgeführt worden sind. Natürlich ist schon festzuhalten, dass naheliegende Gefährdungen zu erfassen und entsprechende Maßnahmen zu setzen sind. Dabei ist die Kenntnis von Regeln der Technik wie Normen und Merkblättern sowie Informationen von Interessenvertretungen von großem Vorteil.
Abschließend ist festzuhalten, dass im Rahmen der Prävention die Hauptstelle der AUVA und dabei insbesondere die Fachgruppe Maschinensicherheit Fachseminare zum Thema Risikobeurteilung von Maschinen anbietet. Speziell das Thema der Risikobeurteilung ist für viele Unternehmen von besonderem Interesse, da in diesen Fachseminaren nicht nur die theoretischen Aspekte behandelt werden, sondern auch der Praxisteil einen breiten Bereich einnimmt, in dem vor allem Lösungskonzepte dargestellt werden. Sollte Ihr Interesse geweckt worden sein, informieren Sie sich näher auf der Website der AUVA unter www.auva.at/sicherheitschulung.
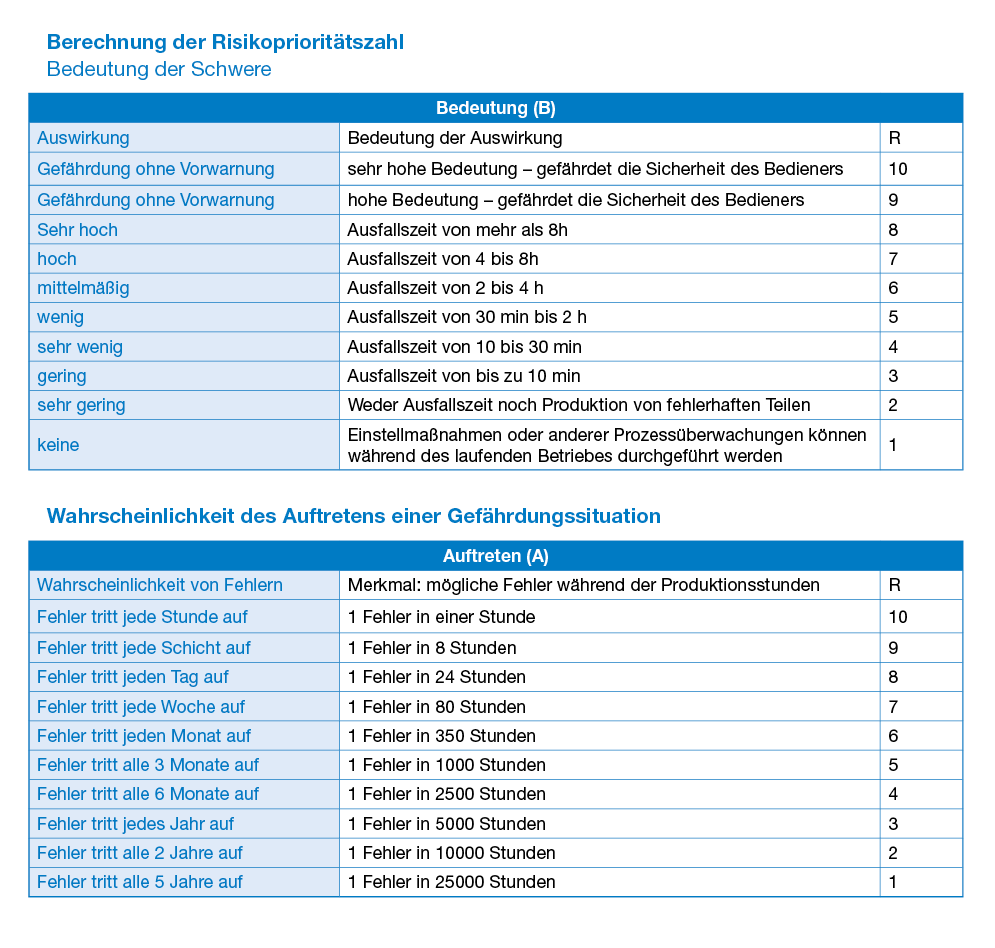
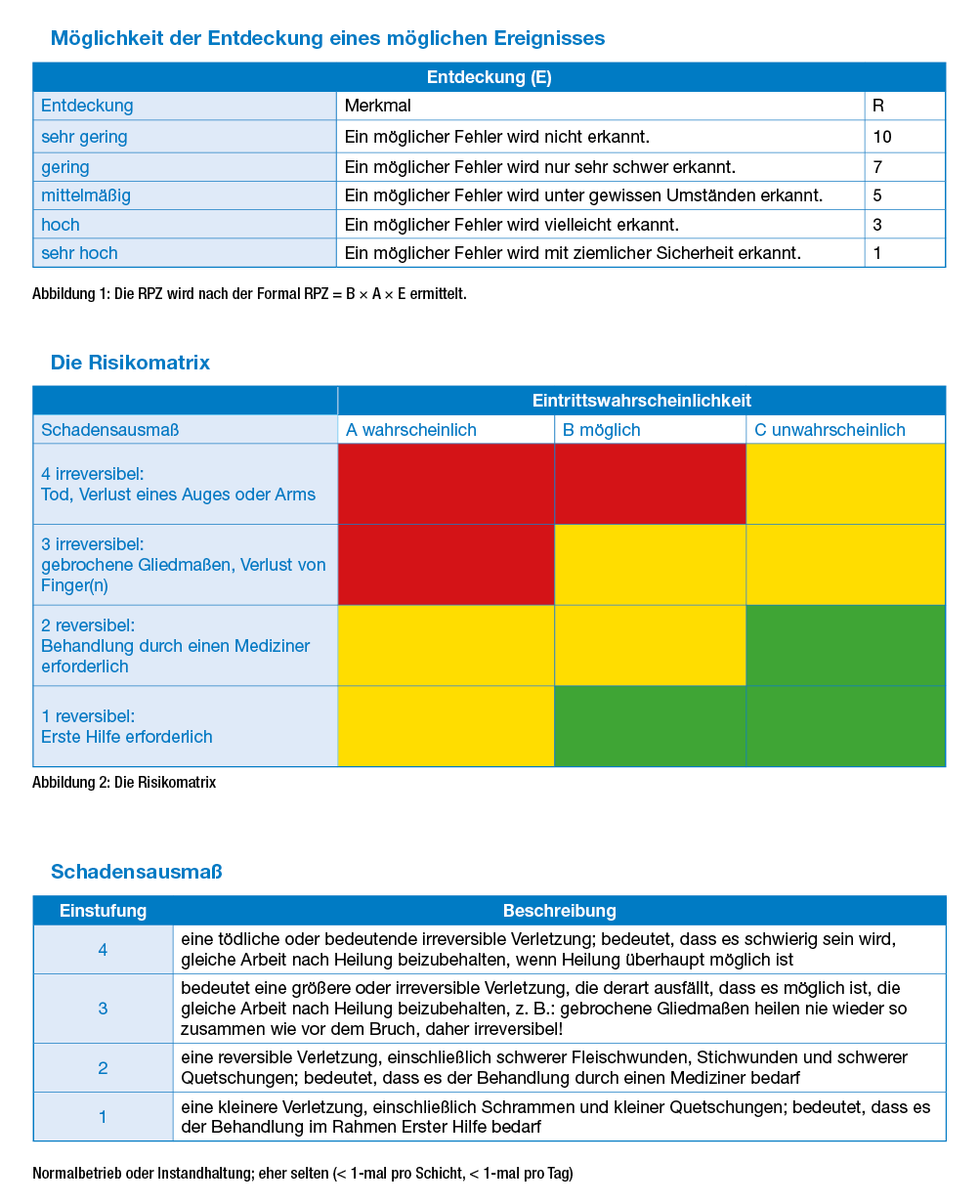
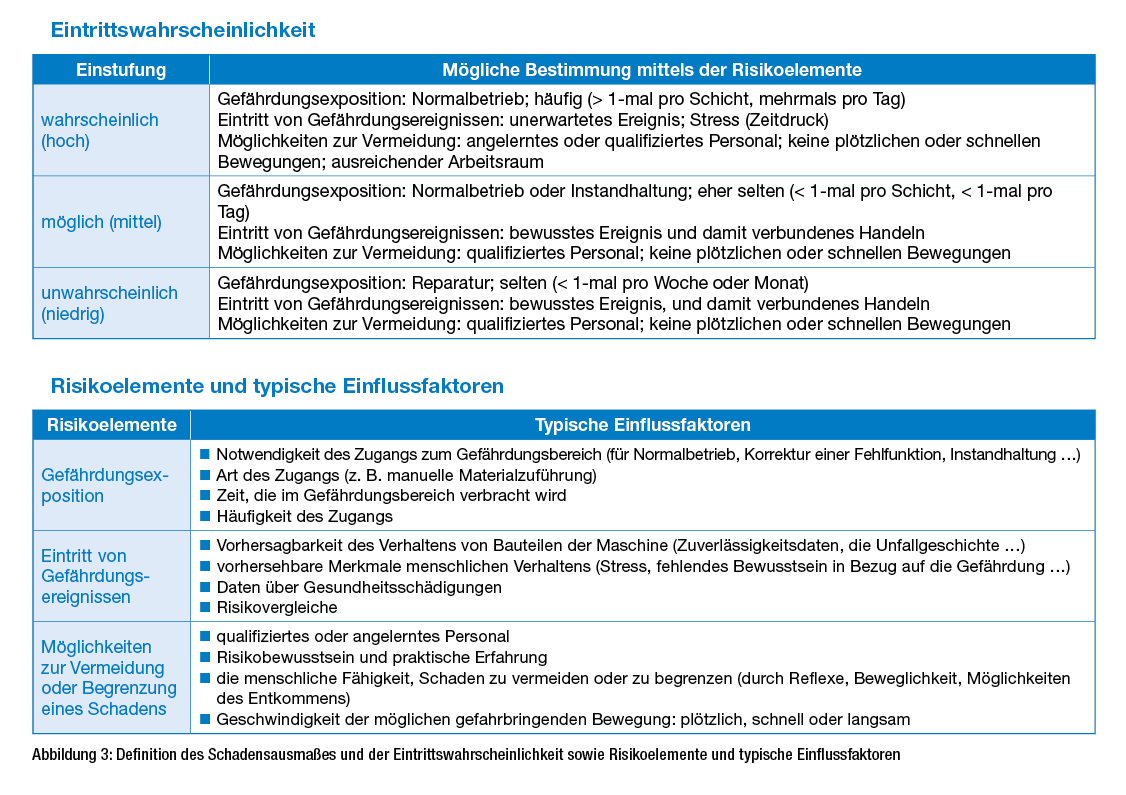
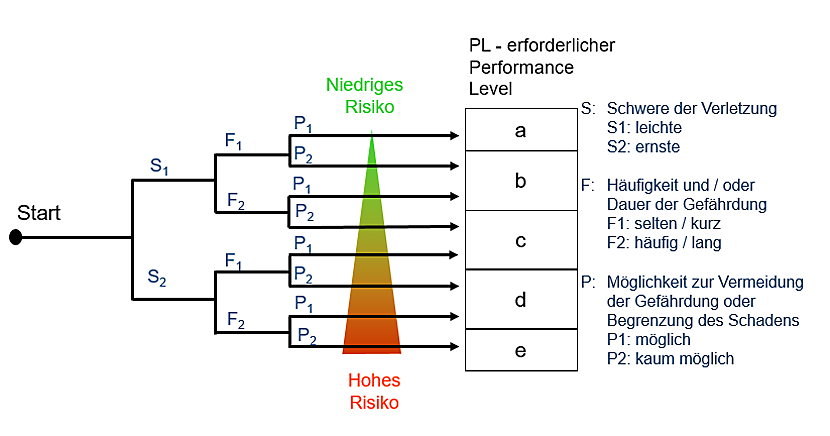
Zusammenfassung
Wie kann man das von Maschinenund Anlagen ausgehende Risiko beherrschen und minimieren? Der Autor zeigt die normativen Rahmenbedingungen auf und beschreibt die gängigen Verfahren der Risikobeurteilung.